AF General says F-35 JIT supply chain wrong. He’s right.
Lt. General Michael Schmidt, F-35 program executive officer, says the Just In Time F-35 parts supply chain is wrong. I can’t agree with him more.
Just In Time, aka JIT, is a principle widely used in modern manufacturing to try and ensure parts arrive as close to when they are needed as possible, reducing the manufacturer’s on-hand inventory and increasing the number of times inventory is turned over (inventory turns are a widely used metric used to judge how efficient your manufacturing is.)
In the private sector, Schmidt said, that kind of efficient supply chain works well for keeping costs low. But in a future war involving highly contested environments, it could lead to disaster, he said.
“When you have that [just-in-time] mentality, a hiccup in the supply chain, whether it be a strike … or a quality issue, becomes your single point of failure,” Schmidt said. “We need to look at, what does ‘right’ look like in the future, to give us more resilience in a combat environment.”
The F-35 enterprise’s sustainment network is “enormous,” Schmidt said, encompassing airplanes operating from 27 bases and 10 ships. Nine nations fly the F-35 operationally, and there are 17 countries in all taking part in the program.
Not sure how many parts are on an F-35, but imagine trying to get all of them arriving where they are needed exactly when they are needed. Sound like a formidable task? It is, and purchasing/scheduling folks world-wide tear their hair out every day trying to make it happen. A couple of basic truths, however:
1) It’s a great process when it works. But something, somewhere in the supply chain, always breaks down.
2) Somebody, somewhere in the supply chain, has to hold inventory. Simple logic tells you that: if you make part with a component that has a 12 week lead time which only ships in bulk, and you have to ship parts weekly, you will hold component inventory.
JIT is a convenient fiction foisted on stockholders to convince them that their manufacturing is lean (which doen’t mean what you think it does, either) and mean – but think of the ideal end result: You only get parts when you need them. What if there are field losses or catastrophic failures in the field you haven’t forecast (a virtual certainty in war)? Where are you going to get those replacement parts that haven’t been manufactured yet?
There’s a reason why they say logistics is what wins wars – if you can’t get bullets to the bullet-launchers, your front lines are equipped with awkward clubs, or maybe short spears. Ditto with replacement airplane parts – war by its nature stresses equipment to its limits, causes unforeseen failures, and stresses supply chains. In turn, that means you have to stockpile parts, not for what is happening, but for what MIGHT happen. JIT is the opposite of that.
We already hear that our full production of artillery rounds is lagging battlefield needs – in one, relatively small, localized conflict. Now we have a tremendously complex fighter with components from an incredible number of sources used in many countries – and we’re set up to have minimal spares capacity? IMO, someone in the Pentagon needs to listen to LGEN Schmidt.
Category: Air Force, Military issues, Pentagon
I work on an unnamed rocket launcher program and I can assure you that there are many supply chain issues. For example, there are subcomponents to things as simple as grounding straps that go obsolete and replacements have to be found, drawings updated and material requalified. Other issues are just going with the wrong supplier sometimes. Places say they can delivery and there is no reason to suspect they wont and then they don’t. When we are making less than 50 launchers a year and the part needed is only one unit per launcher, we aren’t a big chunk of their annual income. That sometimes makes them less likely to care. Fortunately, we have some supplier that bend over backward for us. Since we are just starting out production after a decade+ hiatus, it remains to offload the bad suppliers (if that can be done – talking to you sole sourced parts) and finding the hungry small businesses that want to perform.
JIT? We try to have parts there at least a month prior to need and can accept up to two months prior. Anything less than that would be taking a huge risk.
I can tell you it aint easy. I can’t image what trying to buy all of the fancy shmancy parts for something like the F35 is like. Most of my lead times are from about 6 months to 425 days. Can’t image what F35 parts are like. And we have way less parts than they do.
Back in the late 1970’s there was enough problems getting parts to the fleet to keep aircraft flying without a JIT supply chain.
JIT for military operations is simply idiotic.
The company I worked for in the 90’s tried the JIT supply plan. We in the service department began to referring to it as Just Isn’t There.
JIT us crap. It’s “If you leave it to the last mjnute. It only takes a minute!” made official, justified by “expensive warehousing costs” (you know, PLL) being somehow more intolerable than having parts on-hand. Can’t flex if something bad happens, too. Poor prior planning dressed-up as efficiency.
(Dang it, I hate typing on a frickin’ phone before I’ve had coffee. Y’all know what I mean– JIT sux and Murphy’s Law will kick its ass.)
Don’t be silly. JIT has worked perfectly the last few years. A few more years and everything will be back to normal. It’s right around the corner, you will see.
Speaking of which, domestic passenger vehicle production has risen to nearly 40% of it’s previous peak (yes 40%)… However, it isn’t the vehicles of old. Since they can only make so many they are making only the most expensive ones to get the best profit margin. Which, combined with Obama’s genius plan of throwing away billions of dollars crushing up old cars has created a shortage of passenger vehicles in the US unlike anything seen since WWII.
This has forced the price of used vehicles into the crazy pants range. The truck I bought new in 2019 at a big discount is worth more today than what I paid for it. My car is also worth more, although it is a year old. These violate all the old rules of depreciation. Inflation, she is the crazy chick you hung out with for a few weeks and spent all your money, now she won’t leave.
This is another part of the old America that is passing. The freedom of the open road for everyone.
How left/libtards treat America:
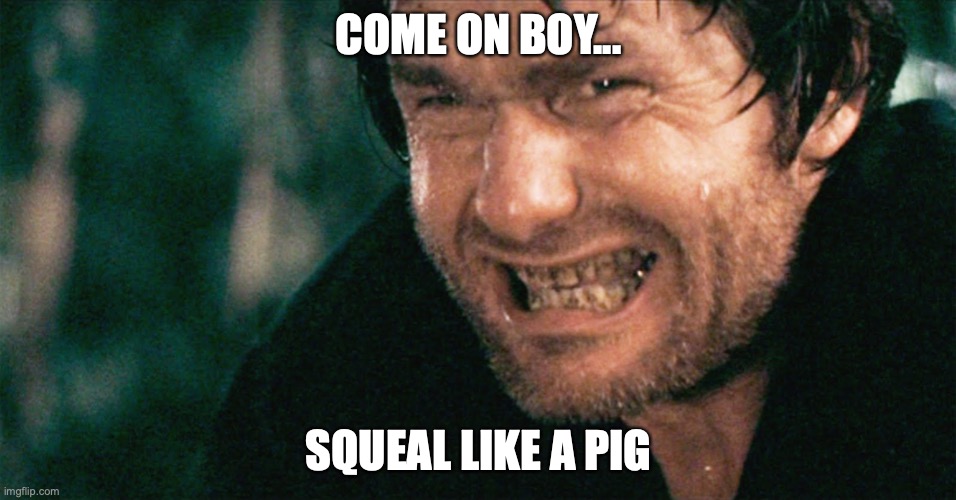
I should be alarmed at this, but I’m not. The F35 is not a war machine, it’s a vote generator for politicians. They cant cancel it without putting voters out of work. If I remember rightly, parts for the thing are made in 35 states. Thats a lot of voters.
F35 Pork Delivery Vehicle– the only weapon system that accomplishes its main purpose in life by just sitting there.
The JIT concept worked oh so well for the automotive manufacturers when the chip shortage hit. That’s why the ultra efficient companies like ford had hundreds of thousands of cars and trucks stored in open fields while they kept the production line going even though they could not complete the vehicles.
Yup. Boeing’s production lines shut down for 20 paid working days when the Saudis dropped a big plane order on ’em and they couldn’t even keep on fakin’ the funk any more like that. That was better than having sh*t on-hand? Nor did folk learn from it.
Gonna bite us square in the azz. Watch.
I have always called the Joint Strike Fighter a jobs program.
JIT for war fighting is stupid. More stupid than McNamara believing the F-111 could work for the USAF and Navy.
I remember the first time I heard about “Just-in-Time”. I was a 21 year-old college drop out and I thought it was the dumbest idea ever. I’m now pushing 50, with 2 bachelor’s degrees (project management and STEM) and 1 course away from completing a MBA, having worked in my industry in everything from being an assembler on the shop floor to selling multi-million dollar electrical power distribution systems. And, you know what, in spite of all those courses on lean manufacturing, TQM, and Six Sigma, I still lean on what my now 28+ years of experience and my lying eyes tell me, JIT is the dumbest fucking idea ever.
When i first heard JIT, i realized it’s not “just in time”. That is a marketing buzzword. (CoughCloudCough)
It’s “efficiency”. That is a valid objective.
So is “resilient”.
So is “adaptable to change”.
And the same damfool marks keep buying 100% “efficiency” snake oil instead of balancing it with resiliency and adaptability.
Because lots of folks go efficiently broke. Or resiliently. Or adaptably.
Because one-trick ponies get old fast.
JIT!? HA!
I work as a technician in a small manufacturing & repair shop.
I’m also the Parts order person.
I know it’s not right (what if I died tomorrow? who would be able to do my job?), but I keep a rolling ROP list in my head.
As I go around the shelves, I see that, “oops, we’re running low, need to order 100-200-500 more”.
And that RoP varies, depending on: frequency of use (in the past year/since last order), projected future use, delivery time from order, cost (do we need approval from higher-ups?).
Even with a RoP system, we’ve still been bitten in the ass. We have several circuit boards that we tried to re-order last year, only to be told, “no-can-do, parts are obsolete, need a total re-design, new parts list, testing, etc”. And that ain’t cheap, nor quick. And so we’ve been struggling with that for the past year.
One circuit board supplier, I don’t trust them as far as I can throw them (don’t ask, long story). I have to do 100% testing, which takes precious time. We’re slowly getting on top of it, but it’s “out” as fast as it’s “in”, no stocking against future use yet.
And now, back to work.
I am not sure what a “just in time” system for repair and maintenance is. Unless you are clairvoyant and can sense the need for parts before you need them you either have an inventory of parts on hand when you need them or you order parts from the manufacturer when you need them. In the second case your vehicle/aircraft/system is “deadlined” until the part is manufactured and shipped
“Just in time” is stupid for a military. War, and even peacetime readiness for war, is expensive. Period. If cutting costs is your priority then just surrender and get it over with. .
One cuts military costs by vanquishing the enemy, thus reducing the need to spend so much.